Definition, Formula, & Benchmark
What's Keeping Your Customers Waiting?
DIFOT (Delivery In Full On Time) is Australia's preferred term for what globally is known as OTIF on-time in full – the critical supply chain metric that separates thriving businesses from those struggling with customer dissatisfaction and operational inefficiencies.
Picture this: A customer places an order, eagerly anticipating its arrival, only to receive an incomplete shipment three days late. The frustration is palpable, the trust eroded, and the likelihood of repeat business diminished. This scenario plays out countless times across supply chains worldwide, highlighting the critical importance of delivering orders correctly and punctually.
In today's competitive marketplace, customer satisfaction hinges on one fundamental promise: delivering exactly what was ordered when it was promised. This is where DIFOT (or OTIF globally) becomes the ultimate measure of supply chain excellence.
Whether you're managing logistics operations, overseeing supply chain processes, or striving to improve supply chain visibility, understanding and optimising your OTIF performance can transform your business from struggling with customer dissatisfaction to achieving operational excellence that drives customer loyalty and business growth.
What is OTIF and Why Should You Care?
Improve Supply Chain Visibility
.jpg)
OTIF on time in full is a critical supply chain metric that measures a supplier's ability to deliver complete orders within agreed timeframes. This comprehensive measure evaluates two essential components: temporal accuracy (delivering on time) and quantity accuracy (delivering in full). The concept gained prominence. Walmart formalised OTIF as a mandatory supplier KPI in 2017 as a key performance indicator to track supplier performance, drive operational improvements, and increase customer satisfaction across its entire supply chain.
The significance of time in full OTIF extends far beyond simple delivery tracking. It serves as a barometer for supply chain operations effectiveness, revealing how well your supply chain management systems coordinate to meet customer demand. When you measure OTIF consistently, you're essentially evaluating your organisation's reliability in fulfilling delivery promises, which directly impacts customer satisfaction and long-term business performance.
This supply chain metric has become increasingly vital as market demands continue to evolve. Customers expect not just competitive pricing but also reliable service that consistently delivers on-time deliveries without compromising on order completeness. The beauty of OTIF lies in its simplicity and comprehensiveness - it provides a holistic view of your supplier's ability to meet commitments, encompassing everything from raw materials procurement to final delivery across your entire supply chain.
Ready to Eliminate OTIF Challenges? Let's Talk
Our comprehensive third-party logistics provider, 3PL services in Sydney and Melbourne, streamlines your operations with reliable solutions. Contact us now!
Calculate OTIF: Breaking Down the Numbers That Matter
Understanding the OTIF On Time in Full Calculation & Formula
.jpg)
To calculate OTIF effectively, you need to understand the fundamental formula that drives this crucial measurement. The OTIF formula is straightforward yet powerful:
OTIF Rate = (Total deliveries made on time and in full / Total deliveries made) × 100
For example, if your company processes 800 orders in a month and 680 arrive at the correct location within the confirmed delivery time, containing all requested items, your OTIF rate would be (680/800) × 100 = 85%.
However, calculating OTIF isn't always as simple as it appears. The challenge lies in defining what constitutes "on time" and "in full." Different retailers and supply chain partnerships may have varying interpretations - some consider delivery within a specific delivery window acceptable, while others require delivery on the exact confirmed delivery time. This lack of a standard OTIF definition creates complexity in supply chain management as manufacturers struggle to meet diverse retailer requirements.
The timing component requires careful consideration of lead time expectations and delivery delays, while factors such as supply chain disruptions and logistics challenges can significantly impact your ability to maintain consistent on-time deliveries. Similarly, the "in full" component depends on accurate inventory management, efficient warehouse management systems, and robust supply chain visibility to ensure complete order fulfilment without compromising your OTIF calculated results.
Good OTIF Benchmark: Setting Realistic Performance Targets
Establishing Standards for Good OTIF Score and Performance
In Australia, a DIFOT above 95 per cent is generally expected, while world-class performers aim for 97-99 per cent. Although 100 per cent perfection is the ideal, real-world supply chains face variables—long distances, sparse population centres and extreme weather - that make lead-time adherence the main OTIF failure mode.
Walmart’s programme illustrates how benchmarks evolve: the US retailer raised its supplier threshold from 75 per cent in 2017 to 98 per cent today, backed by a 3 per cent cost-of-goods penalty for non-compliance.
Illustrative OTIF/DIFOT targets by ABC inventory class
(actual targets are always contract-specific)
- Class A (high-value / high-volume): 97–99 %
- Class B: 92–96 %
- Class C (low-value / long-tail): 80–90 %
The financial stakes are significant: a 2019 McKinsey study on OTIF in the consumer sector estimated US $5-6 billion in annual OTIF penalties across the US consumer-packaged-goods sector. Australian retailers do not yet levy OTIF-specific charge-backs, but the upcoming Supplier Protection Code enables fines of up to A$10 million for wider supply-chain breaches.
Regional variations - network infrastructure, regulations and customer expectations - mean each business should calibrate “good” OTIF against its own lane lengths, partner SLAs and cost-to-serve economics.
The Hidden Costs of Low OTIF Scores
Beyond Numbers: Real Business Impact on Inventory Levels
.jpg)
Low OTIF scores create ripple effects throughout your organisation that extend far beyond immediate delivery performance issues. The most visible impact is customer dissatisfaction, which manifests through negative reviews, increased customer service inquiries, and reduced customer loyalty. When customers experience late or incomplete deliveries repeatedly, they lose confidence in your brand's reliability, often leading to customer churn and reduced lifetime value.
The financial implications of poor OTIF performance are multifaceted and substantial. Direct costs include retailer penalties, expedited shipping charges to correct delayed deliveries, and inventory holding costs for products that couldn't be delivered as planned. Supply chain disruptions often compound these effects, as partners throughout your network lose confidence in your operational efficiency, resulting in less favourable contract terms and reduced priority during capacity constraints.
Poor OTIF performance also reveals underlying weaknesses in supply chain processes, indicating inadequate inventory levels, inefficient warehouse operations, poor demand forecasting, or insufficient supply chain visibility. The reputational damage from consistently poor performance can be particularly challenging to overcome, as customers readily share negative experiences through social media and review platforms, making customer acquisition more expensive and retention increasingly difficult.
Improve OTIF: Proven Strategies to Boost Performance & Customer Satisfaction
Transform Your Supply Chain Performance Through Strategic Improvements
Improving OTIF performance requires a comprehensive approach that addresses multiple aspects of supply chain operations. Here are the key strategies that can transform your delivery performance:
- Implement Robust Warehouse Management Systems: Deploy advanced systems that provide real-time visibility into inventory levels, order status, and potential delays. These systems enable proactive management of supply chain processes and help identify potential delays before they impact customer satisfaction.
- Optimise Inventory Management: Maintain optimal stock levels across distribution centres to ensure customer demand can be met without stockouts or backorders. Advanced demand forecasting techniques, combined with safety stock optimisation, help balance inventory holding costs with service level requirements.
- Enhance Supply Chain Visibility: Implement real-time tracking and monitoring systems that enable early identification of potential issues. Track shipments throughout the delivery process to proactively communicate with customers about delays and take corrective action to minimise impact.
- Deploy Automation Technologies: Reduce human error and increase operational efficiency through automated order processing systems that eliminate manual data entry errors. Automated picking and packing systems improve accuracy and speed, whilst robotics and AI-driven logistics processes enhance consistency.
- Design Strategic Distribution Networks: Position inventory closer to customers through multiple fulfilment centres to reduce delivery distances and lead times. This distributed approach provides redundancy that helps maintain service levels during supply chain disruptions.
- Establish Continuous Improvement Programmes: Implement regular performance reviews, root cause analysis of failures, and systematic process improvements to create a culture focused on operational excellence. Collaborate with logistics companies and supply chain partners to facilitate shared learning and coordinated improvement efforts.
Transform Your Delivery Performance Today
Implementing these OTIF improvement strategies requires expertise and infrastructure. Our end-to-end logistics solutions leave all your fulfilment needs with us. Get in touch with us today!
Measure OTIF: Tools and Techniques for Accurate Assessment
Implementing Comprehensive OTIF Measurement Systems
Effectively measuring OTIF requires sophisticated tracking systems and methodologies that capture accurate data across all aspects of your supply chain operations. Here are the essential tools and techniques for a comprehensive OTIF assessment:
- Integrated Warehouse Management Systems: Modern systems that integrate with transportation management platforms to provide end-to-end visibility of order progress from receipt through final delivery. These systems automatically track key performance indicators and generate real-time reports for immediate response to emerging issues.
- Real-Time Data Collection: Implement daily or real-time measurement systems that allow for quick identification and resolution of problems before they escalate. Accurate timestamps for order receipt, processing, and delivery are essential for meaningful analysis.
- Integrated Business Systems: Ensure integration between customer relationship management systems, enterprise resource planning platforms, and logistics management tools to maintain data consistency and eliminate discrepancies that could skew OTIF calculations.
- Segmented Performance Analysis: Conduct granular analysis across different product categories, customer segments, and geographic regions to identify specific areas requiring attention and enable targeted improvement initiatives.
- Advanced Analytics and Machine Learning: Deploy algorithms that analyse historical performance data, weather patterns, traffic conditions, and other variables to forecast delivery challenges and recommend preventive actions. Transform OTIF measurement from reactive reporting to proactive management.
- IoT Sensors and Tracking Devices: Implement the Internet of Things sensors throughout your supply chain to provide real-time data on shipment location, condition, and estimated arrival times for granular visibility and proactive exception management.
Inventory Management: The Foundation of OTIF Success
Optimising Stock Levels for Consistent Performance
Effective inventory management & forecasting serve as the cornerstone of achieving consistently high OTIF scores. Without adequate stock levels strategically positioned throughout your distribution network, even the most efficient logistics processes cannot deliver complete orders on time. Strategic inventory positioning across multiple distribution centres reduces lead times and improves the likelihood of on-time deliveries by analysing customer demand patterns and geographic distribution to optimise placement and minimise shipping distances.
Safety stock calculations must balance the cost of carrying excess inventory against the risk of stockouts that damage OTIF performance. Advanced forecasting techniques that incorporate seasonal variations, promotional activities, and market trends help determine optimal safety stock levels for different product categories. Real-time inventory visibility across your entire supply chain enables proactive management of stock levels and helps prevent situations that could compromise OTIF performance.
Demand forecasting accuracy directly impacts your ability to maintain appropriate inventory levels for optimal OTIF performance. Statistical forecasting models that incorporate multiple variables - including historical sales data, market trends, and promotional plans - provide more accurate predictions than simple trend analysis. Machine learning algorithms can continuously refine these forecasts based on actual performance, improving accuracy over time and ensuring your inventory investment supports your OTIF goals while minimising carrying costs.
Improving OTIF Performance: Advanced Strategies and Technologies
Leveraging Technology and Innovation for Superior Results
The integration of advanced technologies represents the next frontier in improving OTIF performance. Here are the key technologies and strategies that are transforming supply chain operations:
- Internet of Things (IoT) Integration: Deploy IoT sensors throughout your supply chain to provide real-time data on shipment location, condition, and estimated arrival times. This granular visibility enables proactive management of exceptions and helps maintain customer satisfaction even when unexpected delays occur.
- Artificial Intelligence and Machine Learning: Implement algorithms that analyse vast amounts of supply chain data to identify patterns and optimise operations for better OTIF performance. These systems predict demand fluctuations, optimise routing decisions, and recommend inventory adjustments based on historical performance and external factors.
- Collaborative Planning Platforms: Establish shared forecasting, coordinated promotional planning, and integrated inventory management with supply chain partners to reduce the variability that challenges OTIF performance. Strong partnerships built on mutual trust create resilient networks that maintain high performance during disruptions.
- Blockchain Technology: Leverage immutable records of transactions and shipment movements to create transparency that helps identify bottlenecks and inefficiencies. While still emerging, blockchain applications show promise for improving the accuracy and reliability of OTIF measurement.
- Employee Training and Engagement Programmes: Ensure technological investments translate into operational improvements through comprehensive training. Well-trained staff who understand the importance of OTIF performance are more likely to make decisions that support operational excellence.
- Predictive Analytics Systems: Deploy systems that use historical data, weather patterns, and market conditions to forecast potential delivery challenges before they occur. This proactive approach transforms supply chain management from reactive to predictive.
Scale Your Success with Professional Fulfilment
Our fulfilment services delight your customers with seamless order orchestration and transparent pricing, allowing you to plan better with predictable fulfilment costs. Contact us today!
Ready to Master Your OTIF Performance?
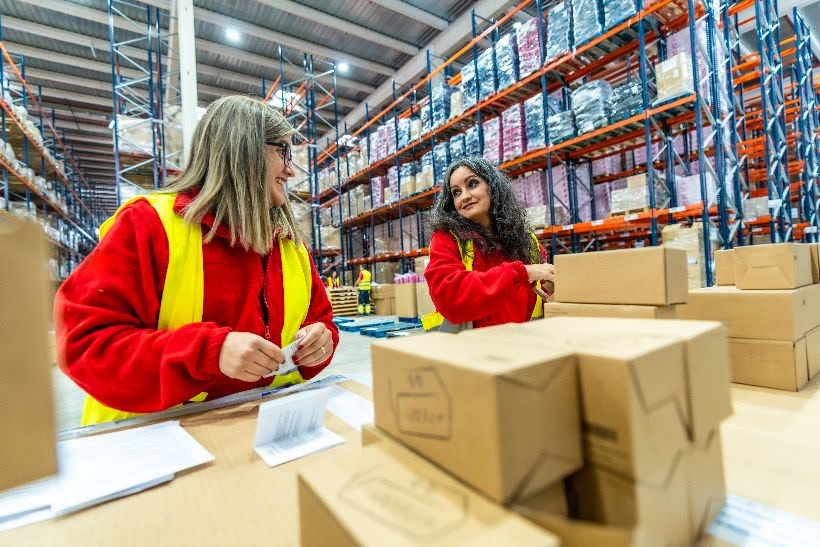
Mastering OTIF on time in full performance is not merely about achieving statistical targets – it's about building a supply chain that consistently delights customers and drives sustainable business growth. The strategies and insights outlined in this comprehensive guide provide a roadmap for transforming your supply chain efficiency from reactive to proactive, from good to exceptional. By implementing robust OTIF measures and focusing on full deliveries across your distribution centres, you can overcome common OTIF challenges that plague modern logistics operations.
The journey to excellent, on-time performance requires commitment, investment, and persistence in tracking essential OTIF metrics that reveal operational strengths and weaknesses. Companies that excel at OTIF performance gain significant competitive advantages through their ability to improve customer satisfaction and maintain reliable delivery promises.
As customer expectations continue to evolve and market demands become increasingly sophisticated, the importance of comprehensive OTIF measures will only grow, making it essential to assess performance regularly and adapt to changing conditions.
The path forward involves continuous improvement, technological innovation, and an unwavering focus on operational excellence that addresses all OTIF challenges systematically. By implementing the strategies discussed in this guide and maintaining a commitment to superior in full deliveries, your organisation can achieve the high OTIF metrics that distinguish industry leaders from their competitors. Remember, achieving excellent OTIF performance is an ongoing journey rather than a destination, requiring regular assessment and adaptation to maintain the supply chain efficiency that drives long-term success.